Process / Quality Assurance Monitoring
Process control is all about measuring temperatures and/ or determining the shape of certain products on a production line. The acquired data is used to control and improve the process so that the temperatures or shapes are according to specification.
For many applications, such as the production of parts and components for the automotive or electronics industry, thermal data are critical. While machine vision can see a production problem, it cannot detect thermal irregularities. Thermal imagery provides much more information to production specialists and decision makers. Indeed, for non-contact precision temperature measurement there is nothing to equal thermal imaging. It adds a new dimension to machine vision and is the perfect solution for applications involving non-contact precision temperature measurement and non-destructive testing.

Metal Manufacturing
Heat treatment is used in metal manufacturing to alter the chemical and physical properties of the resulting metal parts. Careful application of a specific sequence of heating and cooling cycles for predetermined intervals enables metallurgists to control the parts’ hardness or softness. Thermal imaging can be used to monitor the temperature of metal parts after leaving a cooling bath, or “quench pit.”

Automotive Manufacturing
New vehicles are subjected to many individual and automated quality control tests. Many automobile manufacturers are using thermal imaging cameras for quality control. Typical applications include inspection of rear window heating, heated seats, checking exhaust flaps, air-conditioning outlets, and more.
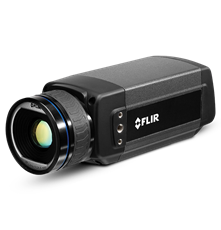

Electronic Components
Cutting down failure rates of electronic components is essential for companies that want to supply a flawless product to their customers. The only way to ensure this is by checking each individual component to provide 100 percent quality control. Thermal imaging enables electronic components manufacturers to detect hot spots, which are indicative of defective products.

Food Processing
In the food industry, it’s essential to carefully control the temperature and shape of perishable goods throughout production, transportation, storage, and sales. Food processors need tools that automate crucial operations in a way that helps minimize human error while holding down costs.
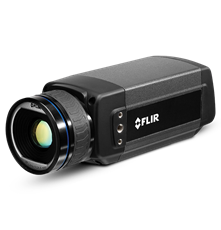

Packaging
Thermal imaging cameras make a clear distinction between what is hot and what is not. This, combined with emissivity effects, sometimes allows thermal imaging cameras to “see through” plastic or other material to confirm adhesive placement for packaging.
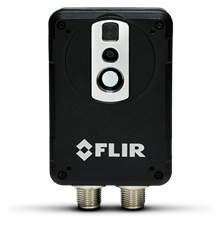

Adhesion
Clear or black glue applied to a black background is very difficult for a visible light camera to see and measure. FLIR automation infrared cameras, however, can easily determine whether the glue bead has been applied properly, has gaps and even if it is within the allowable temperature limits. FLIR thermal imaging is also integral to adhesive bonding using induction, a trending process in the automotive industry.
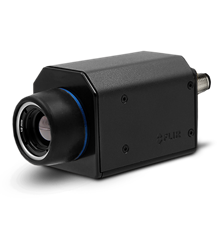

IR Welding
Infrared welding is a heat-based joining technique that creates a very strong bond. But inconsistencies in heating, subsurface defects, and other anomalies can cause an incomplete or bad weld pattern. Because thermal imaging cameras can visualize the IR weld as it’s applied, it allows manufacturers to monitor the weld process as it happens and verify the weld quality without pulling pieces apart for spot-checks.